- Verpackung
- Lagerung
- Automatisierung
„Automatisch besser packen?“ Optimierung und Automatisierung im E-Commerce-Lager
Über Chancen und Einsparpotenziale automatisierter Verpackung – auch bei mittleren Versandmengen.
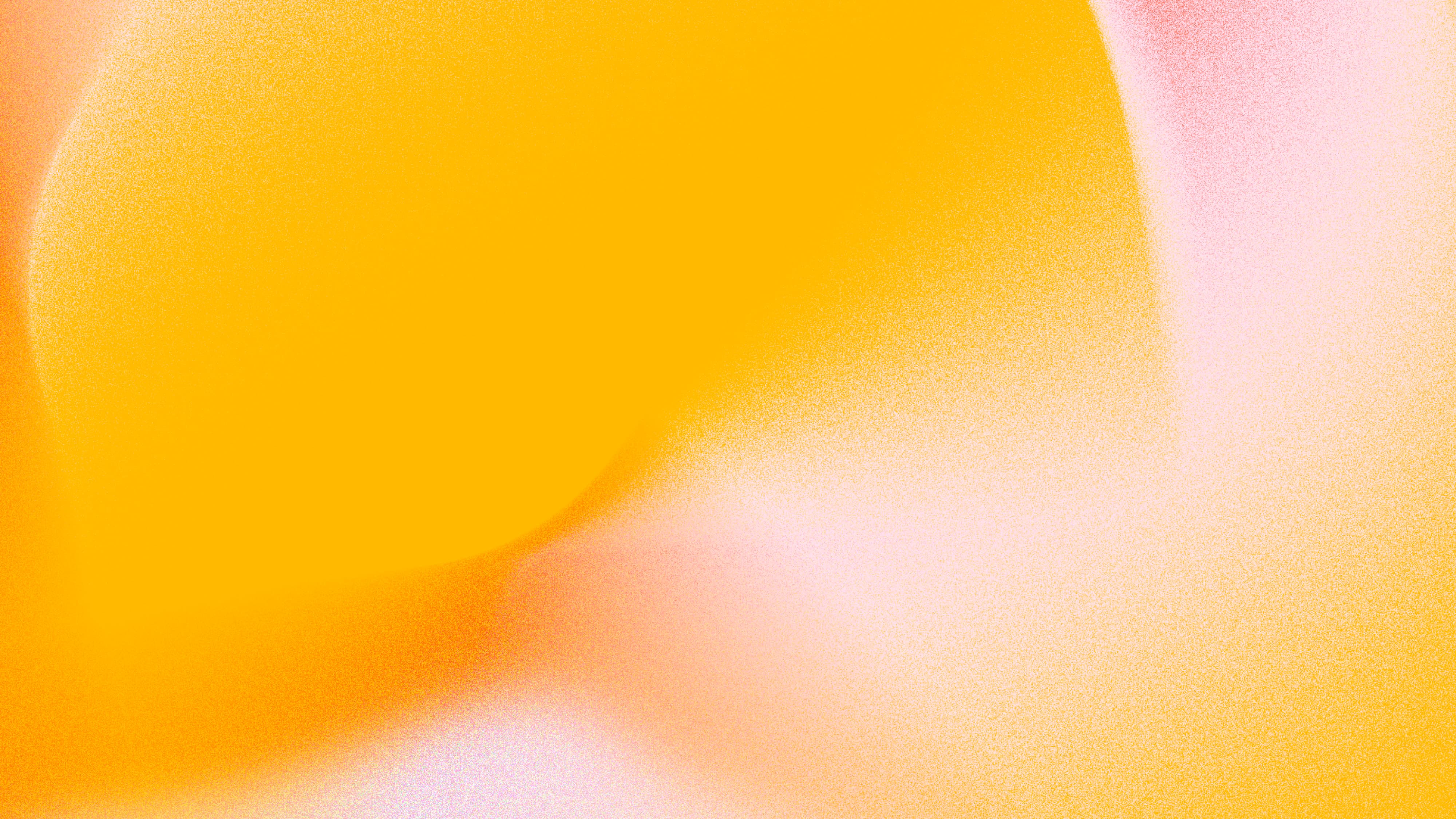
In a nutshell: Verpackungsprozesse sind ein entscheidender Faktor für Effizienz und Kosten im E-Commerce. Mit steigenden Versandvolumina stellt sich für viele Unternehmen die Frage: Lohnt sich eine Automatisierung? Man glaubt der Durchsatz muss besonders hoch sein, aber das stimmt gar nicht. Mit ein paar Hundert Paketen pro Tag kann eine automatische Verpackungslösung erhebliche Einsparungen bringen – von geringeren Personalkosten über reduzierten Materialverbrauch bis hin zu einer verbesserten Prozessqualität. Während vollautomatische Systeme hohe Effizienz bieten, erfordern sie eine sorgfältige Wartung und eine größere Anfangsinvestition. Halbautomatische Lösungen sind flexibler, erreichen aber nicht die gleiche Geschwindigkeit. Angesichts der stetig wachsenden Paketmengen und steigender Nachhaltigkeitsanforderungen setzen immer mehr Unternehmen auf smarte Verpackungsautomation – eine Investition, die nicht nur Kosten senkt, sondern auch die Zukunftsfähigkeit sichert.
Aufwandsverteilung in E-Commerce-Lagern
In einem E-Commerce-Lager bestimmen zwei zentrale Prozesse den operativen Aufwand: die Kommissionierung und die Verpackung. Während das Order-Picking mit rund 50 bis 55 % der Lagerarbeitszeit den größten Zeit- und Kostenfaktor darstellt, nimmt auch das Verpacken eine bedeutende Rolle ein. Analysen zeigen, dass etwa 20 % der gesamten Arbeitszeit in Lager und Distribution auf diesen Bereich entfallen. Die restlichen Tätigkeiten verteilen sich auf Wareneingang, Einlagerung, Versandbereitstellung und administrative Aufgaben.
Personalkosten machen mit bis zu 70 % den größten Anteil an den Lagerkosten aus. Besonders der manuelle Prozess des Pickens und Packens treibt diese Kosten in die Höhe. Während Kommissionierung als Hauptkostentreiber gilt, verursacht auch das Verpacken erhebliche Aufwände – sowohl durch Arbeitszeit als auch durch den Verbrauch von Verpackungsmaterialien wie Kartonagen, Füllmaterial und Klebeband. Typischerweise entfallen zwischen 8 und 15 % der Fulfillment-Kosten auf den Verpackungsprozess. Angesichts dieser Kostenstruktur stellt sich die Frage, inwiefern eine Optimierung oder Automatisierung der Verpackungsprozesse sinnvoll sein kann.
Wann lohnt sich die Automatisierung der Verpackung?
Mengenschwelle: Eine vollautomatische Verpackungsmaschine lohnt sich in der Regel erst ab einem gewissen Versandvolumen. Branchenbeispiele zeigen, dass sich eine Investition bereits ab ca. 800 Paketen pro Tag rentieren kann. Auch die Verpackungsanlagen-Hersteller berichten, dass ab ~800 Sendungen/Tag ein guter Business Case für automatisches Verpacken besteht. Viele Unternehmen glauben fälschlicherweise, man bräuchte „tausende Pakete pro Tag“ für Wirtschaftlichkeit – tatsächlich liegt die Schwelle oft darunter. Wichtige Einflussfaktoren für die Wirtschaftlichkeit sind:
- Personalkosten: Hohe Lohnkosten begünstigen die Automation, da Maschinen Arbeit von mehreren Packmitarbeitern ersetzen können. Eine automatische Anlage arbeitet etwa 20-mal schneller als eine manuelle Packstation, wodurch pro Schicht deutlich mehr Sendungen abgefertigt werden können.
- Kostenersparnisse: Automatische Maschinen fertigen passgenaue Kartons an. Dadurch sinken die Versandkosten (weniger Volumen, mehr Pakete pro LKW) und der Materialverbrauch (kaum Füllmaterial, optimierter Zuschnitt). Diese Einsparungen fließen in die ROI-Berechnung ein.
- Investitionskosten und ROI: Moderne Verpackungsautomaten haben typischerweise eine Amortisationszeit von 2–3 Jahren (24–36 Monate). In Einzelfällen wurde sogar ein ROI < 12 Monaten erreicht, wenn die Einsparpotenziale (Personal, Porto, Material) besonders groß waren.
- Volatilität und Wachstum: Unabhängig vom aktuellen Paketvolumen investieren viele Versender präventiv in Automatisierung, um für künftiges Wachstum und Peaks gerüstet zu sein. Schwankende Nachfragen (z. B. Saisongeschäft) können mit einer Maschine leichter abgefangen werden, da sie Lastspitzen effizienter bewältigt.
- Weiche Faktoren: Aspekte wie Prozessqualität (gleichbleibende Packqualität, weniger Fehler) und Nachhaltigkeit (kleinere Pakete = weniger CO₂) spielen ebenfalls eine Rolle. Eine automatisierte Lösung ermöglicht oft nachhaltigeres Verpacken, was dem Unternehmensimage und Kundenanforderungen entgegenkommt
Investition in eine Verpackungsmaschine: Eine Beispielrechnung
Was bei jedem Automatisierungsprojekt zählt, sind die Kosten bzw. der ROI (Return on Investment). Genauso stellt sich auch bei Verpackungsprozessen die Frage, ob sich die Investition lohnt oder eben nicht. Hierbei kommt es auf eine genaue Analyse der Stückkosten an – also darauf, welche Kosten pro verpacktem Paket entstehen.
Bevor eine Verpackungsmaschine angeschafft wird, sollten Unternehmen also eine umfassende Kosten-Nutzen-Analyse durchführen. Dazu zählen unter anderem die Anschaffungskosten, laufende Betriebskosten und natürlich der Vergleich zur manuellen Verpackung (dem IST-Prozess).
Investitionskosten (Beispielhafte Zahlen)
Die Anschaffung einer Verpackungsmaschine ist mit hohen initialen Kosten verbunden:
- Maschine: ca. 765.000 €
- IT-Integration: ca. 45.000 €
- Gesamtkapitalbedarf: ca. 810.000 €
Laufende Kosten pro Jahr
Neben den Investitionskosten müssen auch die jährlichen Betriebskosten berücksichtigt werden:
- Abschreibung (AFA) über 8 Jahre: ca. 101.250 €
- Zinskosten (4 % p.a.): ca. 15.300 €
- Wartungskosten (variabel, je nach Hersteller/Maschinentyp)
- Gesamtkosten pro Jahr: ca. 116.550 €
Vergleich: Manuelle vs. automatische Verpackung
Der Hauptfaktor für die Rentabilität ist die Stückkostenbetrachtung, also die Kosten pro verpacktem Paket. Dabei zeigt sich ein erheblicher Unterschied zwischen der manuellen und der automatischen Verpackung:
- Manuelle Verpackung: 20 Pakete pro Stunde, Kosten pro Paket: ca. 2–3 € (höhere Lohnkosten)
- Automatische Verpackung: 300 Pakete pro Stunde, Kosten pro Paket: ca. 1,67 €
Wann lohnt sich die Investition?
Die Automatisierung kann sich insbesondere dann lohnen, wenn die Einsparungen durch reduzierte Personalkosten, geringeren Materialverbrauch (das wird gern vergessen) und optimierte Logistikprozesse die Investitionskosten übersteigen. Ein Unternehmen sollte daher eine detaillierte Kalkulation durchführen und dabei auch Faktoren wie Skalierbarkeit, Produktionsspitzen und langfristige Effizienzsteigerungen berücksichtigen.
Ein einfaches Rechenbeispiel verdeutlicht dies:
- Angenommen, ein Unternehmen verpackt täglich 5.000 Pakete.
- Bei manueller Verpackung (2,50 € pro Paket) entstehen Kosten von 12.500 € pro Tag.
- Bei automatischer Verpackung (1,67 € pro Paket) liegen die Kosten nur bei 8.350 € pro Tag.
- Ersparnis: 4.150 € täglich, was hochgerechnet auf ein Jahr über 1,5 Mio. € Einsparung bedeutet.
Diese Berechnung zeigt, dass sich die Investition in eine Verpackungsmaschine bereits innerhalb weniger Jahre amortisieren kann. Entscheidend bleibt jedoch, eine realistische Kalkulation der eigenen Betriebsprozesse und zukünftigen Wachstumschancen vorzunehmen.
Herausforderungen und Wartungsanforderungen von Verpackungsanlagen
Komplexität vollautomatischer Systeme: Vollautomatische Verpackungsmaschinen sind hochkomplexe Anlagen, die mehrere Schritte in einem durchgängigen Prozess vereinen: Vermessung der Artikel, Zuschnitt des Kartons, Falten/Verkleben, Wiegen und Labeldruck. Diese Integrationen machen den Prozess ultraschnell, erfordern jedoch präzise Abstimmung und zuverlässige Technik. Die Erfahrung zeigt: Maschinen sind nicht unfehlbar, daher hat ein reibungsloser Betrieb oberste Priorität. Stillstand einer Verpackungsanlage kann den Versand direkt ausbremsen, was in Spitzenzeiten kritisch ist. Entsprechend hoch sind die Anforderungen an Wartung und Betreuung: Unternehmen benötigen ein umfassendes Service- und Wartungskonzept, inklusive Fernsupport, Vor-Ort-Service, präventiver Wartungen, intensiver Mitarbeiterschulungen und regelmäßiger Software-Updates, um den maximalen Nutzen aus der Automation zu ziehen. Die Wartungsintervalle sind planmäßig einzuhalten (z. B. Austausch von Verschleißteilen wie Messer, Förderelemente, Druckköpfe), um ungeplante Ausfälle zu vermeiden. Außerdem sollte man genügend Ersatzteile vorhalten, da spezielle Komponenten Lieferzeiten haben können.
Vergleich halbautomatische Systeme: Halbautomatische Verpackungsmaschinen kombinieren menschliche Arbeitsleistung mit Maschinentechnik. Typischerweise muss ein Mitarbeiter z. B. den Karton manuell anlegen oder den Packvorgang anstoßen, während die Maschine Teilprozesse automatisiert (z. B. Karton zufalten oder siegeln). Diese Geräte sind einfacher aufgebaut und dadurch weniger wartungsintensiv. Vorteile halbautomatischer Systeme: geringere Investitionskosten und höhere Flexibilität bei unterschiedlichen Packgrößen. Zudem sind sie oft robuster im Sinne von weniger komplexer Elektronik – was weniger potenzielle Fehlerquellen bedeutet – und sie lassen sich schneller auf neue Formate umrüsten. Die Wartung beschränkt sich meist auf mechanische Komponenten (z. B. Heißklebegerät reinigen, Messer tauschen) und ist vom Betriebspersonal einfacher zu bewältigen. Allerdings können halbautomatische Lösungen nicht das volle Einsparpotenzial bieten: Da weiterhin manuelle Schritte nötig sind, erreichen sie nicht die Geschwindigkeit vollautomatischer Anlagen und bieten keine 100%ige Prozesskonsistenz. Für sehr hohe Durchsätze oder vollständig personalloses Arbeiten sind sie ungeeignet.
Herausforderungen: Bei vollautomatischen Verpackern besteht eine Herausforderung darin, Technik und Logistikprozess eng zu verzahnen. Beispielsweise muss die IT (WMS/Versandsystem) Bestelldaten in Echtzeit an die Maschine liefern (für Labeldruck und Kartongrößenberechnung). Auch müssen Sicherheitsvorkehrungen getroffen werden: Diese Anlagen haben bewegliche Teile, Schneidewerkzeuge und hohe Taktzahlen – Schutzzäune oder Lichtschranken sind nötig, damit Mitarbeiter nicht gefährdet werden. Zudem sollte das Personal speziell geschult sein, um Störungen schnell beheben zu können (z. B. Stau auf dem Förderband lösen, Papiernachschub einlegen). Bei halbautomatischen Maschinen sind diese Anforderungen geringer; sie sind näher an manuellen Packplätzen und benötigen meist nur kurze Einweisungen. Insgesamt gilt: Vollautomaten bringen höhere Effizienz, erfordern aber ein durchdachtes Wartungsmanagement und erfahrenes Personal, während Halbautomaten einen Kompromiss aus Geschwindigkeit und Einfachheit darstellen.
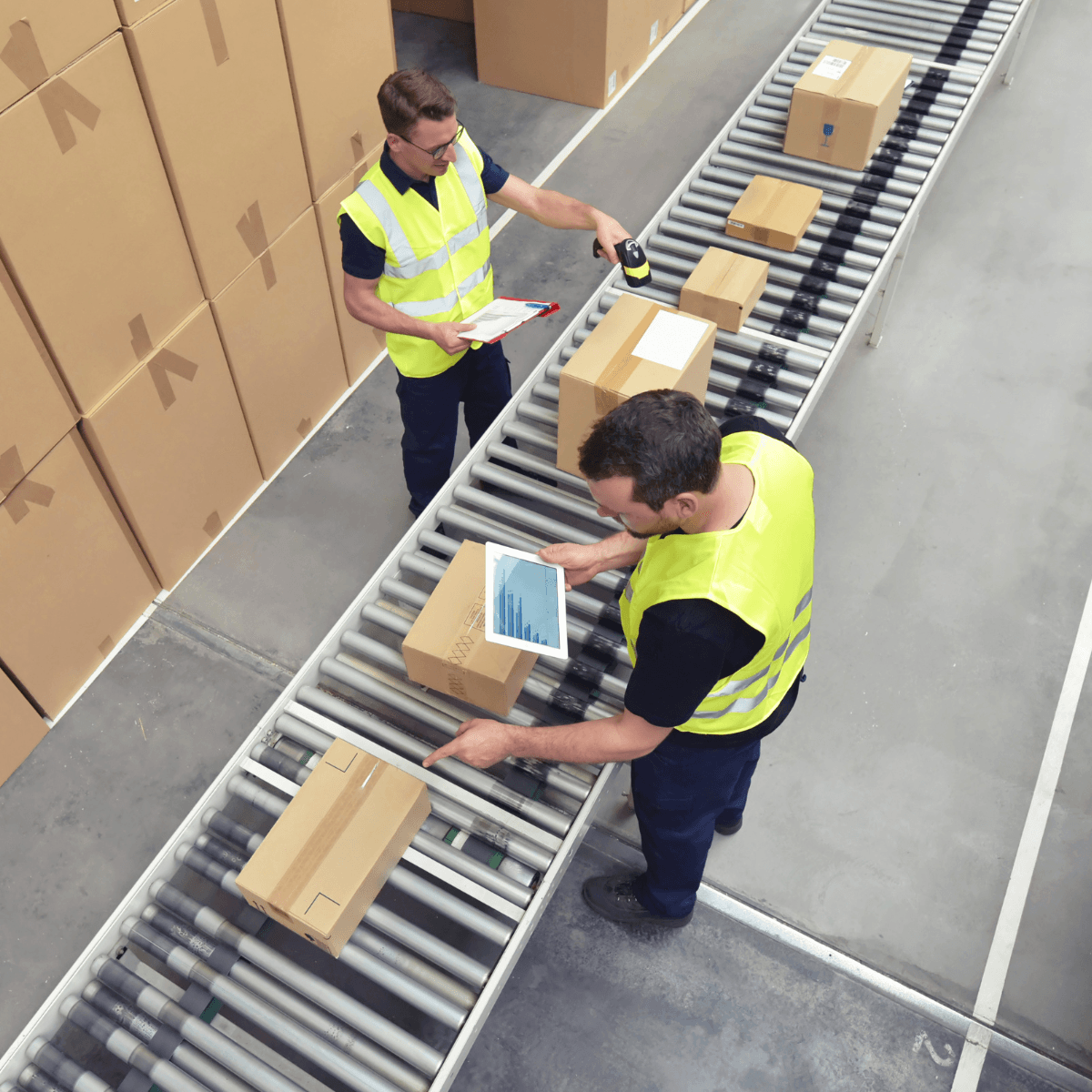
Platzbedarf und Integration automatisierter Verpackungslösungen
Räumliche Voraussetzungen: Automatische Verpackungsmaschinen sind große Anlagen, die entsprechend Platz im Lager erfordern. Je nach Modell kann der Platzbedarf variieren. Beispielsweise hat eine gängige automatische Verpackungsanlage eine Stellfläche von rund 17,8 × 8,5 Metern – das entspricht etwa 150 m² Grundfläche. Hinzu kommt Freiraum für Wartung und Materialnachschub (z. B. Paletten mit Wellpappe). Auch die Zuführ- und Abführtechnik (Förderbänder) benötigt Platz. Oft wird ein linearer Bereich im Lager dafür vorgesehen, z. B. am Rande der Kommissionierzone oder in der Versandzone, wo die Maschine zentral eingebunden wird. Die Deckenhöhe üblicher Anlagen liegt meist bei <3 m, sodass normale Hallenhöhen ausreichen; jedoch müssen Traglasten des Bodens berücksichtigt werden, da Maschine und Fördertechnik dauerhaft hohe Lasten ausüben können. Zusätzlich müssen Stromversorgung (meist 400V Drehstrom) und Datenanbindungen an der Installationsstelle vorhanden sein.
Integration in Prozesse: Für den Betrieb einer automatischen Verpackungslösung sind Anpassungen sowohl vorgelagert (vor dem Verpacken) als auch nachgelagert (nach dem Verpacken) nötig. Upstream müssen die kommissionierten Artikel geordnet der Maschine zugeführt werden. In der Praxis wird meist ein Förderbandsystem installiert, das die gepickten Aufträge vom Kommissionierbereich zur Verpackungsmaschine transportiert. Häufig werden die Artikel in Behältern oder direkt auf dem Band zur Maschine gebracht. Ein Mitarbeiter (oder bei hoher Automatisierung ein Roboter) legt die Waren auf den Induktionsförderer und scannt den Packzettel bzw. Auftragscode ein. Ab dann übernimmt die Maschine: Sie vermisst die Produkte, erstellt einen passgenauen Karton, verpackt und verschließt diesen, wiegt das Paket und bringt das Versandetikett an. Nachgelagert müssen die fertigen Pakete vom Auslauf der Maschine weitergeleitet werden – typischerweise über Förderbänder direkt zur Versandzone oder zu einer Sortieranlage, die die Pakete z.B. nach Versanddienstleister oder Zielregion verteilt. Wenn zuvor manuelle Packtische genutzt wurden, bedeutet dies eine Layout-Änderung: Statt vieler einzelner Packstationen mit Mitarbeitern konzentriert sich der Prozess auf den automatisierten Pack-Workflow, der in den Gesamtmaterialfluss eingebunden ist.
Prozessumstellungen: Durch die Automatisierung verschieben sich auch Aufgaben: Pick & Pack werden entkoppelt. Picker übergeben die kommissionierten Artikel jetzt früher an das System (z.B. indem sie Behälter auf das Förderband stellen), anstatt jeden Auftrag selbst einzupacken. Dies erfordert eine gute Auftragsplanung, damit die Maschine kontinuierlich ausgelastet ist (Bündelung der Aufträge für die automatische Anlage). Gegebenenfalls müssen Kommissionierstrategien angepasst werden, z. B. dass Multi-Order-Picking genutzt wird und danach die Verteilung auf einzelne Paketaufträge vor der Maschine erfolgt. Außerdem müssen alle Daten (Artikelmaße, Gewichte, Auftragsinformationen) korrekt im System vorhanden sein, damit die automatische Anlage fehlerfrei arbeiten kann. Schulungen der Mitarbeiter sind nötig, damit sie wissen, wie Aufträge der Maschine zu übergeben sind und wie bei Störungen reagiert wird. Auch die vor- und nachgelagerten Pufferzonen sind einzuplanen: Beispielsweise Platz für ungepackte Aufträge vor der Maschine und Flächen für fertige Pakete nach der Maschine, um kurzfristige Zwischenlagerung oder manuelle Eingriffe zu ermöglichen. Insgesamt verlangt die Einführung einer automatischen Packmaschine eine Neuorganisation des Verpackungsprozesses im Lager: vom physischen Layout über IT-Schnittstellen bis hin zur Aufgabenverteilung im Team.
Marktentwicklung und Trends in der Verpackungsautomation
Die Nachfrage nach Verpackungsmaschinen steigt kontinuierlich. 2023 erreichte die Produktion von Verpackungsmaschinen in Deutschland einen Wert von knapp 8 Milliarden Euro, ein Wachstum von 10 % gegenüber dem Vorjahr. Der Markt für E-Commerce-Verpackungslösungen wächst besonders stark, da immer mehr Unternehmen in Automatisierung investieren, um steigende Paketmengen effizient zu bewältigen.
Das Versandvolumen im E-Commerce nimmt weltweit weiter zu. 2022 wurden allein in Deutschland rund 4,15 Milliarden Pakete ausgeliefert, und Prognosen gehen davon aus, dass diese Zahl in den kommenden Jahren auf bis zu 5 Milliarden ansteigen könnte. Global gesehen erreichte der Paketversand 2022 über 160 Milliarden Sendungen und wird bis 2026 voraussichtlich auf über 260 Milliarden anwachsen.
Ein klarer Trend in der Verpackungsautomation ist die Entwicklung hin zu passgenauen Verpackungslösungen, die den Materialverbrauch minimieren und den Versand effizienter gestalten. Zudem werden immer mehr intelligente Systeme mit Machine-Learning-Algorithmen eingesetzt, um den Verpackungsprozess weiter zu optimieren. Händler, die frühzeitig in Automatisierung investieren, können nicht nur Kosten senken, sondern sich auch für zukünftiges Wachstum und höhere Anforderungen an Effizienz und Nachhaltigkeit rüsten.
Fazit: Für einen mittelgroßen E-Commerce-Versender (mehrere hundert Pakete täglich) kann sich die Anschaffung einer Verpackungsmaschine lohnen, sofern die oben genannten Faktoren positive Einsparungen versprechen. Unterhalb dieser Schwelle (z. B. < 500 Pakete/Tag) sind halbautomatische Lösungen oder manuelle Prozesse meistens noch kosteneffektiver. Allerdings sollte man abseits vom Business Case den Wartungs- und Integrations-Aufwand einer vollautomatischen Verpackungsmaschine nicht unterschätzen. Und genügend Platz wäre eine gute Idee, denn den hat meist kaum ein Logistiker im Übermaß.
Auf der Suche nach einer passenden Lösung für deine Logistik? Hier geht's zur Vergleichsplattform, die dir die Suche erleichtert.
Quellen:
- Statista: Digitalisierung der Logistikbranche
- Bitkom-Studie: Einsatz von KI und Predictive Analytics in der Logistik
- Gartner Report: Trends in der datengetriebenen Supply Chain
- Deloitte: Effizienzgewinne durch Echtzeit-Tracking und Automatisierung
- VDMA-Bericht: Verpackungsmaschinen-Industrie
- BIEK KEP-Studie 2023: Paketvolumina
- Pitney Bowes Parcel Shipping Index: Entwicklung globaler Paketvolumina
- EHI Retail Institute: Optimierungspotenziale in der Versandlogistik
- Handelsverband Deutschland (HDE): Prognosen zur Marktentwicklung