- Aus der Praxis
- Lagerung
- Automatisierung
Die Schlüsselfaktoren für erfolgreiche Automatisierungsvorhaben bei Lorenz
Über Herausforderungen und die richtige Vorgehensweise bei Logistikerweiterungen anhand der Wahl eines geeigneten Lagersystems.
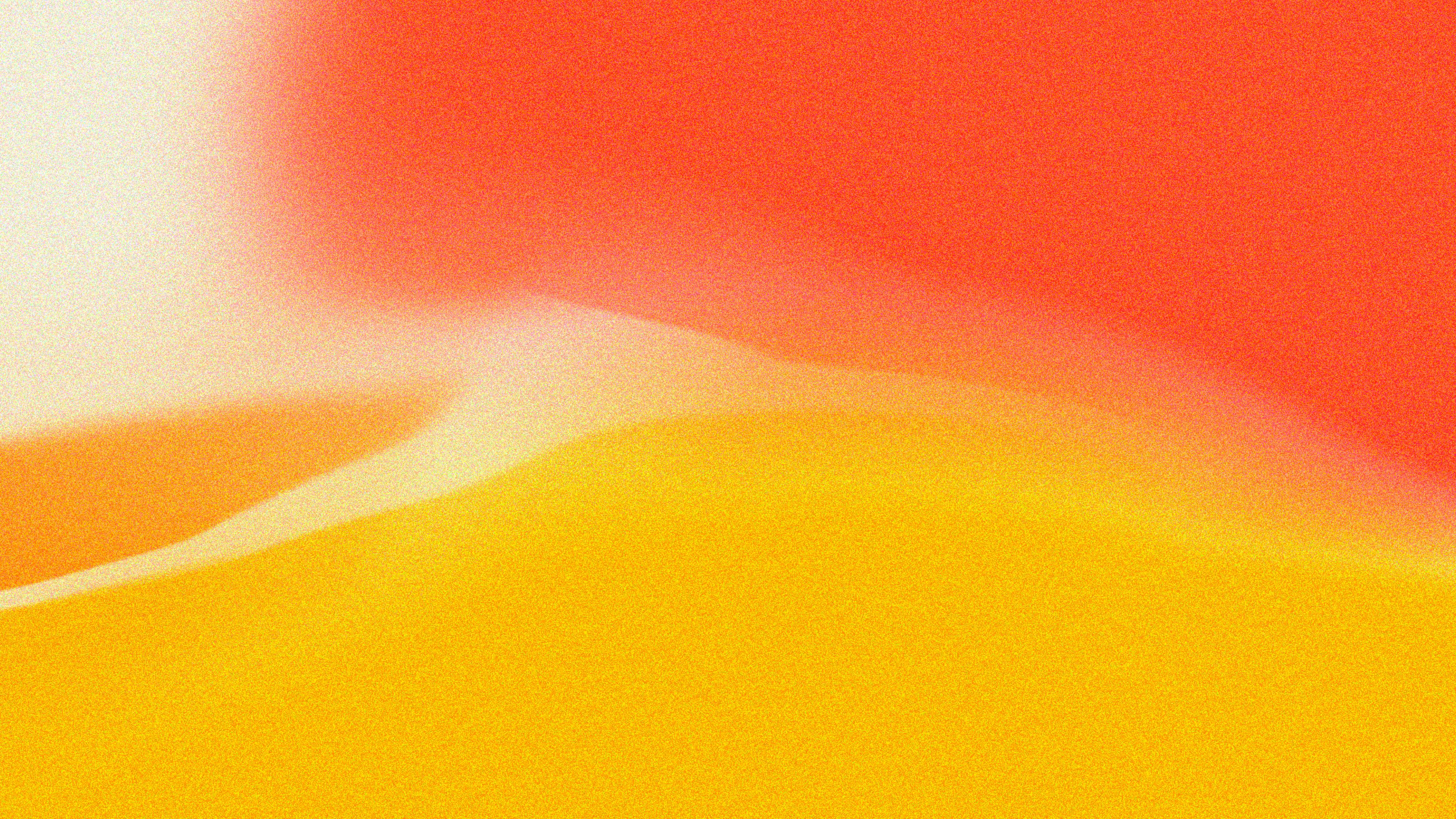
In a nutshell: Wir bei Lorenz wissen aus eigener Erfahrung, wie herausfordernd Automatisierungsprojekte in der Logistik sein können – gerade, wenn es um die Auswahl eines passenden Lagersystems geht. In diesem Beitrag zeige ich euch, wie wir bei Logistikerweiterungen vorgehen und welche Schritte unserer Erfahrung nach essenziell sind. Mein Ziel ist es, euch mit praxisnahen Tipps zu unterstützen und Orientierung zu geben, damit ihr ähnliche Vorhaben erfolgreich umsetzen könnt.
Starre manuelle Prozesse und dauerhaft hohe Lagerbestände – nicht nur saisonal, sondern das ganze Jahr über – sind Herausforderungen, mit denen viele Logistik-Verantwortliche vertraut sind. Auch wir bei Lorenz setzen uns intensiv mit diesen Themen auseinander. Unsere Snacks werden rund um die Uhr produziert und müssen zuverlässig bereitgestellt werden. Eine Auslagerung in externe Außenlager wäre für uns jedoch keine Option – zu teuer, zu ineffizient und vor allem nicht nachhaltig. Deshalb müssen wir prüfen, wie wir das Handling unserer Waren langfristig am bestehenden Standort optimieren können, und beschäftigen uns dabei mit der Automatisierung unserer Logistik.
Der Weg zur passenden Lösung kann jedoch sehr komplex sein und hängt von verschiedenen Faktoren ab: Welche Technologien kommen überhaupt infrage? Welche Kriterien sind entscheidend? Und vor allem: Wie bindet man die Mitarbeitenden ein, damit die neue Lösung nicht nur technisch, sondern auch praktisch funktioniert? Diese 5 Schlüsselfaktoren sind entscheidend für die erfolgreiche Umsetzung eures Automatisierungsvorhabens:
1. Netzwerk- und Bedarfsanalyse
Bevor eine Lösung implementiert werden kann, muss klar sein, was genau optimiert werden soll. Dafür ist eine umfassende Analyse essenziell:
- Stellplatzbedarf im Wachstum berücksichtigen: Wo stehen wir aktuell? Welche Prognosen gibt es für die Zukunft? Wo wollen wir langfristig hin?
- Optimale Lagerreichweite definieren: Kurze Abrufzeiten müssen gewährleistet sein, um eine effiziente Lieferbereitschaft sicherzustellen.
- Klare Ziele setzen: Möchten wir Kosten reduzieren, die Genauigkeit verbessern, die Effizienz steigern oder nachhaltiger arbeiten?
- Relevante Stakeholder frühzeitig einbeziehen: Neben Logistik und Management sind auch IT, Planung, Produktion und Engineering entscheidend für den Erfolg des Projekts.
2. Technologieauswahl
Nach der Analyse folgt die Entscheidung für ein geeignetes Lagersystem. Dabei sind verschiedene Faktoren zu berücksichtigen:
- Automatisierte Lagersysteme evaluieren: Welche Systeme gibt es, und welches passt am besten zu unseren Anforderungen?
- Erstellung einer Evaluationsmatrix mit folgenden Kriterien:
- Investitionskosten: Wie hoch sind die einmaligen Anschaffungskosten und welche laufenden Betriebskosten fallen an? Hier müssen auch mögliche Förderungen oder steuerliche Vorteile berücksichtigt werden.
- Zugänglichkeit: Wie einfach können Waren im laufenden Betrieb entnommen oder hinzugefügt werden? Gibt es Einschränkungen durch das System?
- Durchsatz: Wie viele Ein- und Auslagerungen kann das System in einer bestimmten Zeit bewältigen? Entspricht das der benötigten Kapazität?
- Flexibilität: Kann das System bei sich ändernden Anforderungen (z. B. Wachstum, neue Produktlinien) angepasst werden oder ist es zu starr?
- Raum- und Flächennutzung: Nutzt das System den vorhandenen Raum optimal oder gibt es Alternativen, die eine effizientere Nutzung ermöglichen?
- Anforderungen an die Bodenqualität: Manche Systeme benötigen spezielle Böden oder Tragfähigkeiten – ein wichtiger Punkt in der Planungsphase.
- Zusätzliche Technologien einbeziehen: Die Auswahl des Lagersystems ist nur ein Teil der Lösung. Genauso wichtig ist die Abstimmung mit anderen Technologien:
- Lagerverwaltungssysteme (LVS): Ein modernes LVS muss nahtlos mit dem Lagersystem interagieren können. Hier ist zu prüfen, welche Anbieter passende Schnittstellen bieten und wie flexibel diese Systeme anpassbar sind.
- IoT-Lösungen: Sensoren, Echtzeit-Tracking und automatisierte Datenerfassung können Prozesse erheblich optimieren. Die Frage ist, wie gut das gewählte System diese Technologien unterstützt und wie Daten integriert werden.
- Robotik: Werden Fördertechnik oder autonome Transportroboter integriert? Welche Steuerungssoftware ist erforderlich und wie lassen sich diese Lösungen in bestehende Systeme einbinden?
Welches Lagersystem am besten geeignet ist, lässt sich demnach nicht pauschal beantworten und hängt von euren spezifischen Anforderungen ab.
3. Wissenstransfer und Erfahrungsaustausch
Erfolgreiche Automatisierungsprojekte basieren auf fundiertem Wissen und praktischer Erfahrung:
- Stakeholder-Einbindung: Mitarbeitende aus IT, Logistik und Management sollten in den Entscheidungsprozess einbezogen werden, um alle relevanten Perspektiven zu berücksichtigen.
- Externer Austausch: Der Blick über den Tellerrand hilft enorm. Gespräche mit Unternehmen, die bereits automatisierte Lagersysteme betreiben, ermöglichen es, von Best Practices zu lernen.
- Wissen gezielt ins Unternehmen holen: Fehlendes Know-how kann durch gezielte Neueinstellungen oder Schulungen ausgeglichen werden.
- Erfahrungswerte vergleichen: Der Vergleich verschiedener Lösungen ist oft nicht leicht, da Systeme in unterschiedlichen Umgebungen unterschiedlich performen. Hier können Vergleichsplattformen wie even logistics hilfreich sein, um auf reale Erfahrungswerte zurückzugreifen.
4. Grundflächenbedarf und Standortfrage
Die beste Technologie bringt wenig, wenn der Platz fehlt. Bei uns musste deswegen auch schon das ein oder andere Projekt wieder verworfen werden. Parallel zur Technologieauswahl muss also geprüft werden, welche Grundstücksfläche verfügbar ist.
- Hochregallager als Platzsparer: Besonders in urbanen Gebieten oder bei begrenztem Platzangebot ist die vertikale Nutzung eine optimale Lösung.
- Standortplanung: Ist eine Erweiterung vor Ort realistisch, oder muss möglicherweise ein anderer Standort in Betracht gezogen werden?
5. Personal einbinden und weiterentwickeln
Automatisierung kann den Fachkräftemangel entschärfen, ersetzt jedoch nicht das Personal. Selbst ein automatisiertes Lager benötigt geschultes Fachpersonal.
- Frühzeitige Einbindung der Mitarbeitenden: Die Akzeptanz steigt, wenn sie von Beginn an Teil des Projekts sind.
- Schulung und Weiterentwicklung: Die neue Technologie bringt neue Anforderungen mit sich – das Personal muss im Umgang mit den Systemen vertraut gemacht werden.
- Technik als Werkzeug, nicht als Lösung: Nur mit gut ausgebildeten Fachkräften wird Automatisierung zur nachhaltigen Wettbewerbssteigerung beitragen.
Fazit
Ein Automatisierungsprojekt in der Logistik erfordert eine strukturierte Vorgehensweise. Von der Bedarfsanalyse über die Technologieauswahl bis hin zur Einbindung der Mitarbeitenden – jeder Schritt ist entscheidend für den Erfolg. Durch eine fundierte Planung, den gezielten Wissenstransfer und die richtige Balance zwischen Technik und Mensch kann ein Lager effizienter, nachhaltiger und zukunftssicher gestaltet werden.
Auf der Suche nach einer passenden Lösung für deine Logistik? Hier geht's zur Vergleichsplattform, die dir die Suche erleichtert.