- Intralogistik
Für wen eignen sich Automatische Kleinteillager?
Wie AKLs funktionieren, welche Vorteile und Nachteile sie haben und welche Branchen mit ihnen profitieren.
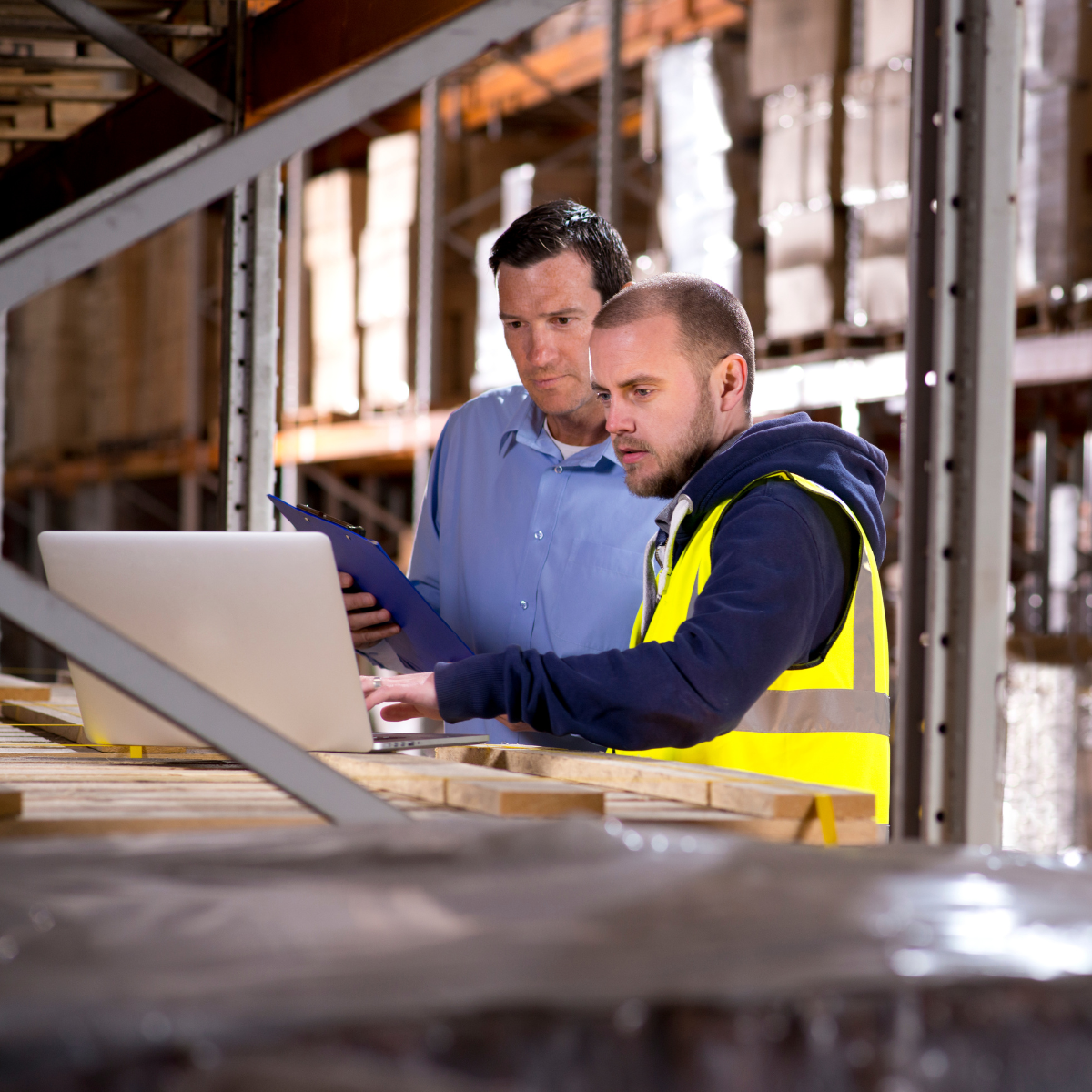
In a nutshell: Ein Automatisches Kleinteilelager (AKL) ist eine spezialisierte Lagerlösung, die darauf ausgelegt ist, kleine bis mittelgroße Artikel in Behältern, Schachteln oder Trays effizient zu lagern und zu verwalten. Artikel können dadurch schnell und präzise an den gewünschten Lagerort transportiert oder von dort abgerufen werden. Diese Technologie ist besonders relevant für Branchen mit hoher Artikelvielfalt, in denen Effizienz, Platzersparnis und Prozesssicherheit entscheidend sind.
Funktionsweise eines AKL
Komponenten
- Regalbediengeräte (RBG): Diese automatisierten Geräte bewegen sich vertikal und horizontal entlang festgelegter Schienen zwischen den Regalzeilen, um Artikel ein- und auszulagern.
- Lagerfächer: Modular aufgebaut, um die Größe und Konfiguration an das Artikelspektrum anzupassen.
- Fördertechnik: Wird in der Regel in der sog. Vorzone des AKL eingesetzt und transportiert die Ladeeinheiten des Systems zu den Arbeitsstationen oder alternativ auch in andere Lagerbereiche.
- Kommissionierstationen: Hier werden Artikel für den Versand oder die weitere Verarbeitung zusammengestellt.
- Steuerungseinheit: Koordiniert die Bewegungen der RBG und die Kommunikation der Systemkomponenten.
- Lagerverwaltungssystem (LVS): Das LVS ist kein zwingender Bestandteil eines AKL, wird aber i.d.R. benötigt und kann auch von einem dritten Anbieter kommen.
Der Betrieb eines AKLs folgt dem "Ware-zur-Person"-Prinzip, bei dem die benötigten Artikel automatisch zu einer Kommissionierstation gebracht werden. Dies beginnt mit der Einlagerung, bei der Artikel erfasst und einem Lagerplatz zugewiesen werden. Sobald ein Artikel benötigt wird, transportiert das Regalbediengerät diesen zur Kommissionierstation. Dort wird er entnommen und weiterverarbeitet. Trotz der Effizienz in den Prozessen gibt es Verbesserungspotenzial, besonders in Bezug auf Flexibilität und den Platzbedarf der Systeme.
Vorteile eines AKL
- Effizienzsteigerung: Schnelleres Ein- und Auslagern von Artikeln.
- Platzoptimierung: Verbesserte Nutzung der verfügbaren Lagerfläche.
- Fehlerreduktion: Minimierung menschlicher Fehler und Verbesserung der Bestandsgenauigkeit.
- Verbesserte Sicherheit: Reduziert das Verletzungsrisiko und Schäden an den Artikeln.
Nachteile eines AKL
- Ineffizienz bei leichten Lasten: Tonnenschwere RBGs bewegen oft nur vergleichsweise leichte Behälter (z. B. 50 kg), was die Effizienz infrage stellt. Der Einsatz kann somit ineffizient und ressourcenintensiv sein.
- Teilweise suboptimale Raumnutzung: Auf Grund der breiten Gassen, die das RBG benötigt, um sich zu bewegen.
- Mangelnde Dynamik: RBGs sind nicht besonders flexibel oder dynamisch, was sie in stark wechselnden Umgebungen einschränken kann.
Skalierbarkeit: AKLs sind häufig nur durch eine Weiterung von weiteren Gassen möglich. Das heißt die Kapazität kann nur mit zusätzlichen RBGs erhöht werden (sofern die Länge voll ausgelastet ist). In einer langen Gasse lässt sich auch ein 2. RBG installieren, dies führt jedoch zu mehr Komplexität in der Gassensteuerung.
Für wen eignen sich AKLs?
AKL-Systeme sind relevant für Branchen, die eine hohe Artikelvielfalt haben, aber keine hohen Durchsatzansprüche. Bspw. Ersatzteilgeschäft, Industrieanwendungen oder auch für Nachschubprozesse in dynamischere Systeme. Gute Systeme für hohe Gebäude insbesondere bei Silobauweise.
Fazit
Automatische Kleinteilelager sind eine Schlüsseltechnologie in der Logistik, die Unternehmen ermöglicht, ihre Lageroperationen zu optimieren, die Leistung zu verbessern und gleichzeitig die Betriebskosten zu senken. Durch den Einsatz eines AKL können Unternehmen schnell auf Marktveränderungen reagieren und ihre Wettbewerbsfähigkeit in dynamischen Industrien erhöhen. Je nach Einsatzgebiet weisen AKLs jedoch auch Nachteile auf, was zum Beispiel die Skalierbarkeit oder die Raumnutzung betrifft. In durchsatzintensiven Branchen wie E-Commerce o.ä. wurden AKLs daher teilweise von dynamischen Systemen wie Shuttle, Cube Storage oder mobiler Robotik abgelöst.